Physical Asset Inspection and Diagnosis
With the increasing complexity of modern equipment and infrastructure, traditional maintenance practices are no longer sufficient.
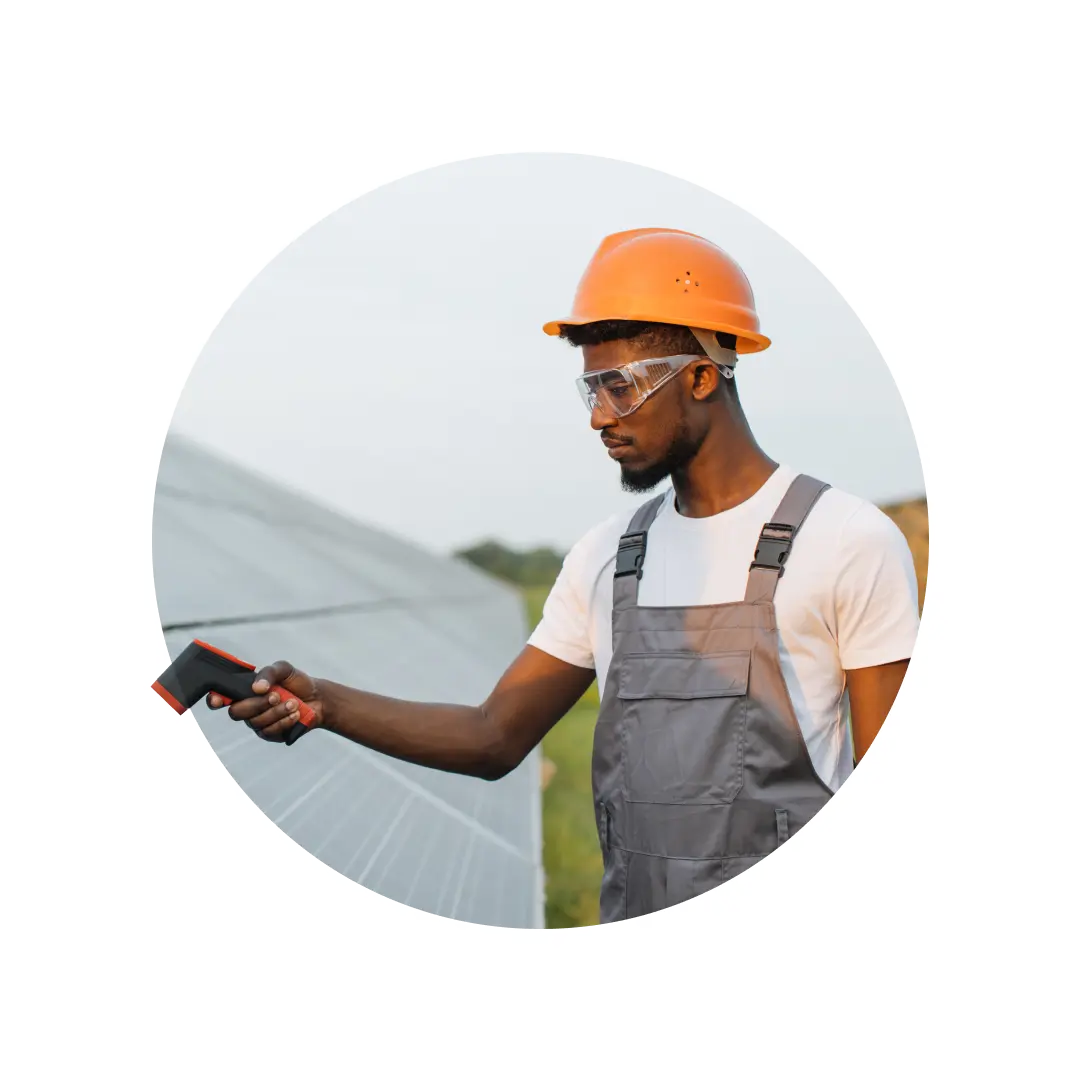
Blog
With the increasing complexity of modern equipment and infrastructure, traditional maintenance practices are no longer sufficient.
Maintenance managers play a critical role in ensuring the longevity and efficiency of physical assets within an organization. With the increasing complexity of modern equipment and infrastructure, traditional maintenance practices are no longer sufficient. To stay ahead, maintenance managers need to embrace physical asset inspection and diagnosis techniques that offer greater sophistication and accuracy. In this blog post, we will explore the importance of inspection and diagnosis, discuss best practices, and highlight the roles of key stakeholders in the process.
Physical asset inspection and diagnosis involve the systematic examination and evaluation of equipment, machinery, and infrastructure to identify potential issues, assess their severity, and recommend appropriate actions. It entails a comprehensive review of various components, such as mechanical, electrical, structural, and operational aspects, to ensure their optimal performance and prevent unexpected failures.
Regular inspections help identify potential risks and mitigate them before they lead to critical failures or accidents.
By detecting early signs of deterioration or malfunctions, maintenance managers can proactively address issues, ensuring the safety of personnel and the integrity of assets.
Timely inspections enable maintenance managers to identify inefficiencies, optimize performance, and reduce downtime. By diagnosing the root causes of problems, managers can develop tailored maintenance strategies, leading to improved asset reliability and increased productivity.
Develop a systematic and well-documented inspection plan that outlines the frequency, scope, and methodologies for each asset.
This plan should consider manufacturer recommendations, regulatory requirements, and historical data on failure modes.
Implement condition monitoring techniques such as vibration analysis, thermal imaging, oil analysis, and ultrasonic testing to detect anomalies and predict failures before they occur. These techniques provide valuable insights into the health of assets and help prioritize maintenance activities.
Internet of Things (IoT) sensors offer real-time data collection and monitoring capabilities. By deploying these sensors on critical assets, maintenance managers can gather valuable information regarding performance, environmental conditions, and usage patterns. This data enables proactive maintenance planning and facilitates predictive maintenance strategies.
Implementing a robust computerized maintenance management system (CMMS) streamlines inspection and diagnosis processes. A CMMS centralizes asset information, schedules inspections, tracks maintenance activities, and generates reports, fostering a data-driven approach to maintenance management.
Prioritize assets based on their criticality and potential impact on operations through a risk-based inspection approach. Consider factors such as asset age, usage, historical data, and safety risks to allocate inspection resources effectively and focus on high-priority assets.
Utilize data analysis and predictive analytics to identify potential failure modes and develop predictive maintenance strategies. Analyze historical data, patterns, and trends to minimize reactive maintenance and optimize resource allocation.
Provide regular training and skill development opportunities for maintenance technicians. Keep them updated with technological advancements and industry best practices to conduct thorough inspections, accurately diagnose issues, and utilize specialized tools effectively.
IoT sensors and maintenance software solutions play a crucial role in enhancing physical asset inspection and diagnosis processes:
With the collaborative efforts of maintenance managers, planners, and technicians, organizations can transform their maintenance practices and achieve long-term success in asset management.
The maintenance manager oversees the inspection and diagnosis process. They develop maintenance strategies, ensure compliance with regulations, allocate resources, and utilize insights from inspections to optimize asset performance.
The maintenance planner collaborates with the maintenance manager to create detailed schedules and coordinate inspection activities. They facilitate communication between maintenance technicians and managers, ensuring inspections are conducted efficiently and in accordance with the maintenance plan.
Maintenance technicians perform hands-on inspections and diagnoses. They follow established procedures, utilize diagnostic tools, and provide accurate data to support decision-making. Technicians are also responsible for implementing maintenance actions, repairs, and ensuring equipment is returned to optimal condition.
Physical asset inspection and diagnosis form the foundation of a proactive maintenance approach. By embracing best practices, such as risk-based inspection, leveraging IoT sensors and maintenance software, and emphasizing continuous improvement and collaboration, maintenance managers can optimize asset performance, minimize downtime, and improve operational efficiency.
Asset inspection and diagnosis FAQs
Learn more about asset inspection and diagnosis
Aquí tienes algunas preguntas frecuentes (FAQs) relacionadas con el mantenimiento correctivo:
El mantenimiento correctivo se refiere al enfoque reactivo de abordar fallos o malfuncionamientos del equipo después de que ocurran. Implica reparar o restaurar el equipo a su estado normal de funcionamiento para minimizar el tiempo de inactividad y asegurar su correcto funcionamiento.
El mantenimiento correctivo se debe realizar cuando se identifican fallos o malfuncionamientos en el equipo. Se activa por averías inesperadas, problemas de rendimiento u otros signos de fallo del equipo que requieren atención inmediata.
El mantenimiento correctivo es un enfoque reactivo que aborda los fallos después de que ocurran, mientras que el mantenimiento preventivo es un enfoque proactivo que busca prevenir fallos mediante inspecciones programadas, tareas de mantenimiento y reemplazo de componentes. El mantenimiento correctivo se realiza como respuesta, mientras que el mantenimiento preventivo se planifica con antelación para mitigar el riesgo de fallos.
Las ventajas del mantenimiento correctivo incluyen la rentabilidad al enfocar los recursos en equipos que realmente requieren atención, minimización del tiempo de inactividad mediante reparaciones rápidas, asignación eficiente de recursos, mayor confiabilidad del equipo a través del análisis de causa raíz, oportunidades de aprendizaje para los equipos de mantenimiento, flexibilidad para abordar fallos imprevistos e integración con estrategias de mantenimiento predictivo.
Las desventajas del mantenimiento correctivo incluyen un aumento del tiempo de inactividad durante las averías de los equipos, potencialmente mayores costes debido a reparaciones urgentes y posibles daños colaterales, riesgos de seguridad, imprevisibilidad en la planificación de actividades de mantenimiento, fiabilidad limitada del equipo, impacto negativo en el cliente y el riesgo de perpetuar una cultura de mantenimiento reactivo.
Las organizaciones pueden optimizar sus esfuerzos de mantenimiento correctivo estableciendo prioridades claras, implementando sistemas eficientes de gestión de órdenes de trabajo, asegurando técnicos capacitados y bien formados, gestionando eficazmente el inventario de repuestos, realizando análisis de causa raíz para fallos significativos, fomentando una cultura de mejora continua, promoviendo la colaboración y comunicación, y midiendo el rendimiento a través de indicadores clave de rendimiento.
Si bien el mantenimiento correctivo es esencial para abordar fallos de equipo, no es suficiente como único enfoque de una estrategia de mantenimiento. Debe complementarse con prácticas de mantenimiento preventivo y predictivo para identificar y mitigar proactivamente posibles fallos, reducir el tiempo de inactividad y optimizar la fiabilidad del equipo.
Ciertos aspectos del mantenimiento correctivo, como la gestión de órdenes de trabajo y el seguimiento del historial de mantenimiento, pueden automatizarse mediante sistemas de gestión de mantenimiento informatizados (CMMS) u otras soluciones de software. Sin embargo, las reparaciones y la resolución de problemas suelen requerir la experiencia de técnicos de mantenimiento cualificados.
El mantenimiento predictivo utiliza análisis de datos y técnicas de monitoreo de condiciones para predecir cuándo es probable que ocurran fallos en el equipo. Al integrar el mantenimiento predictivo con el mantenimiento correctivo, las organizaciones pueden abordar proactivamente los posibles fallos antes de que causen interrupciones significativas o tiempos de inactividad, reduciendo la necesidad de reparaciones reactivas.
La tecnología, como sensores IoT, análisis de datos y software CMMS, desempeña un papel significativo en la mejora del mantenimiento correctivo. Permite el monitoreo en tiempo real, información predictiva, gestión eficiente de órdenes de trabajo, toma de decisiones basada en datos y mejora la comunicación y colaboración entre los equipos de mantenimiento.
Learn more about the inspection and diagnosis universe