What is corrective maintenance?
Corrective maintenance is all about fixing things when they go wrong. It's the reactive side of maintenance, where we address failures, breakdowns, or malfunctions that occur unexpectedly.
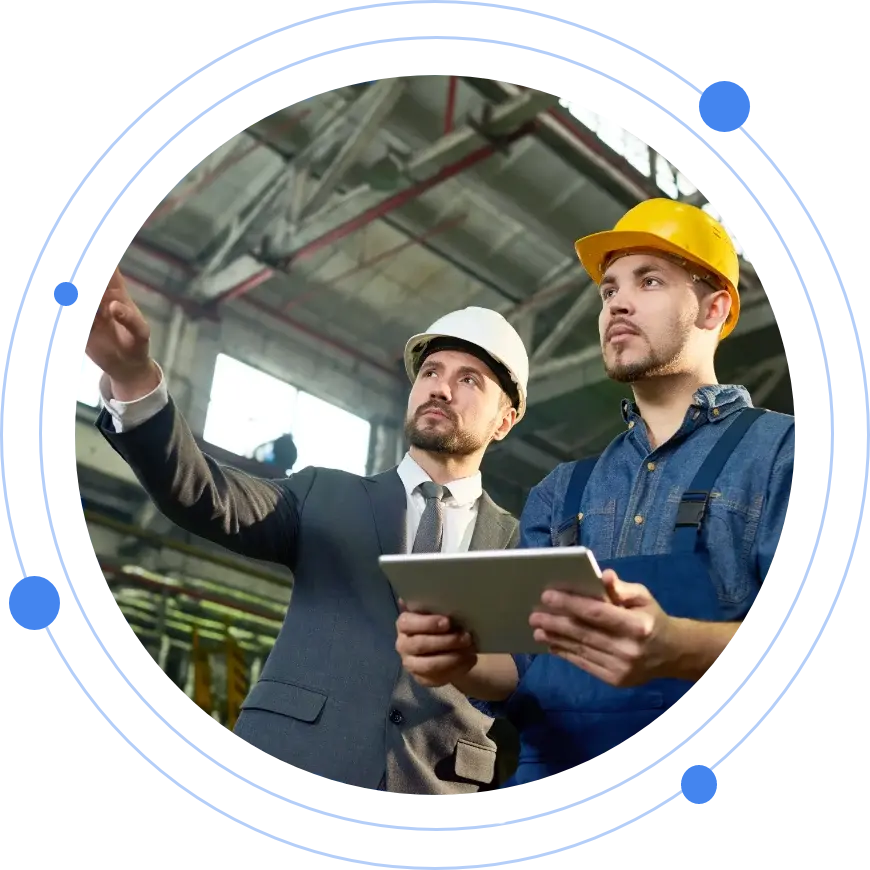
CMMS with AI
Integrations
Blog
Corrective maintenance is all about fixing things when they go wrong. It's the reactive side of maintenance, where we address failures, breakdowns, or malfunctions that occur unexpectedly.
We are diving into the fascinating world of corrective maintenance. Whether you're a seasoned maintenance manager or just curious about the ins and outs of keeping things up and running, this blog post is for you. We'll explore what corrective maintenance is all about, why it's crucial for any organization, and how it can help ensure the smooth functioning of equipment and systems. So, buckle up and get ready for a maintenance adventure!
Picture this: you're in the middle of a busy workday, everything seems to be running smoothly, and suddenly, something unexpected happens. A machine breaks down, a pipe starts leaking, or maybe an electrical system malfunctions. In those frustrating moments, you need a superhero to swoop in and save the day. Well, that's where corrective maintenance comes in.
Corrective maintenance is all about fixing things when they go wrong. It's the reactive side of maintenance, where we address failures, breakdowns, or malfunctions that occur unexpectedly. While preventive maintenance aims to prevent issues in the first place, corrective maintenance is our trusty backup plan when things don't go as planned.
Now, you might be wondering, "Why is corrective maintenance so important?" The answer is simple. In any organization, downtime can be a costly affair. When equipment or systems fail, it can bring productivity to a screeching halt, leading to delays, missed deadlines, and unhappy customers. By promptly addressing these issues through corrective maintenance, we can minimize the impact of unexpected failures and keep operations running smoothly.
Think of it this way: imagine you're driving a car, and suddenly, you hear a strange noise coming from the engine. You could ignore it and hope for the best, but chances are, that noise is an early indication of a problem. By addressing it through corrective maintenance, you can avoid a breakdown on the side of the road. Similarly, in a manufacturing plant, fixing a malfunctioning machine right away can prevent a domino effect of delays and disruptions throughout the entire production process.
Corrective maintenance isn't just about reacting to problems; it's also about learning from them. Each failure or breakdown offers valuable insights into the reliability and performance of our equipment and systems. By analyzing these events, we can identify trends, root causes, and potential areas for improvement. This knowledge can then be used to fine-tune our preventive maintenance strategies, reducing the likelihood of similar issues in the future.
Corrective maintenance comes into play when equipment, systems, or assets experience unexpected failures, malfunctions, or breakdowns. Here are a few situations that call for corrective maintenance:
It's important to note that while corrective maintenance focuses on fixing immediate problems, it's not a long-term solution for preventing future failures. To ensure the reliability and longevity of equipment, a holistic maintenance strategy that includes preventive and predictive maintenance is essential.
By promptly addressing issues through corrective maintenance and learning from each failure, organizations can optimize their maintenance practices, reduce downtime, and enhance overall operational efficiency.
Corrective maintenance encompasses various approaches and strategies to address equipment failures and malfunctions. Let's explore some of the common types of corrective maintenance:
Deferred corrective maintenance refers to postponing the repair or restoration of equipment until a more suitable time. This approach is typically adopted when the failure or malfunction does not immediately impact operations or safety. However, it's important to carefully evaluate the risks and consequences of deferring maintenance to ensure it doesn't lead to more significant issues later on.
Scheduled corrective maintenance involves planning and scheduling repairs during predetermined maintenance windows or when the equipment is not in use. This proactive approach allows for better resource allocation, reduces the impact on production schedules, and enables the efficient allocation of skilled technicians. By incorporating scheduled corrective maintenance into the overall maintenance strategy, organizations can minimize unplanned downtime.
Predictive corrective maintenance utilizes data analysis and condition monitoring techniques to anticipate and address potential failures before they occur. By monitoring key indicators such as equipment performance, temperature, vibration, or fluid levels, maintenance teams can detect early warning signs of impending failures. This approach enables proactive maintenance actions to be taken, preventing unexpected breakdowns and reducing reactive maintenance needs.
Reactive corrective maintenance is performed after an equipment failure or malfunction has already occurred. It involves responding to issues as they arise, addressing the immediate problem, and restoring functionality. While reactive maintenance is often associated with higher downtime and costs, it remains an essential type of corrective maintenance for unforeseen failures.
It's worth noting that organizations may combine different types of corrective maintenance based on the nature of their equipment, operational requirements, and available resources. Striking a balance between proactive and reactive approaches can help optimize maintenance activities and ensure the reliability and availability of critical assets.
Implementing corrective maintenance in a structured and efficient manner is crucial for minimizing downtime, maximizing equipment reliability, and optimizing maintenance resources. Here are some best practices to consider when integrating corrective maintenance into your maintenance strategy:
Develop a clear set of priorities for addressing corrective maintenance tasks. Categorize them based on their impact on safety, production, or other critical factors. This allows you to prioritize urgent repairs and allocate resources accordingly, ensuring that the most important issues are addressed first.
Encourage timely reporting of equipment failures or malfunctions by your team members. Implement a streamlined process for documenting and tracking these incidents. This information will serve as valuable data for identifying patterns, root causes, and opportunities for improvement.
Utilize a computerized maintenance management system (CMMS) or a similar tool to manage work orders for corrective maintenance tasks. This system can help streamline the workflow, track progress, assign tasks to the appropriate personnel, and maintain a centralized repository of maintenance history for future reference.
Ensure that your maintenance team consists of skilled technicians who are knowledgeable in the specific equipment or systems they are responsible for. Invest in training programs to keep their skills up to date and enable them to diagnose and repair failures effectively.
Maintain an organized inventory of spare parts that are frequently needed for corrective maintenance. Regularly review and update the inventory to ensure you have the necessary components readily available. This helps minimize downtime caused by waiting for parts to arrive.
Conduct thorough root cause analysis for significant equipment failures. Identifying the underlying causes of failures helps in implementing corrective measures that prevent recurrence. This analysis can involve techniques like the 5 Whys, fault tree analysis, or fishbone diagrams to dig deep into the root causes.
Continuously assess and refine your corrective maintenance processes. Analyze historical maintenance data, identify trends, and implement preventive actions based on the insights gained. Foster a culture of learning and improvement within the maintenance team to enhance overall efficiency and effectiveness.
Encourage open communication and collaboration between maintenance personnel, operations teams, and other stakeholders. Timely sharing of information about equipment issues, observations, and maintenance requirements can lead to faster response times and better coordination.
Establish key performance indicators (KPIs) to monitor the effectiveness of your corrective maintenance activities. Measure metrics such as mean time to repair (MTTR), equipment uptime, and maintenance costs to evaluate performance and identify areas for further improvement.
Integrate corrective maintenance seamlessly with preventive maintenance practices. Analyze failure data to identify common issues and adjust preventive maintenance schedules accordingly. The goal is to strike a balance between proactive and reactive maintenance approaches for optimal equipment reliability.
By implementing these best practices, you can enhance the efficiency and effectiveness of your corrective maintenance efforts. The key is to establish clear processes, leverage technology where applicable, empower your maintenance team, and continuously strive for improvement.
Corrective maintenance, when implemented effectively, offers several advantages that contribute to the overall efficiency and effectiveness of maintenance operations. Let's explore some of the key benefits:
Corrective maintenance, when applied strategically, offers numerous advantages that contribute to effective maintenance management. By minimizing downtime, optimizing resource allocation, and fostering a culture of continuous improvement, organizations can enhance operational efficiency, extend equipment life, and deliver optimal performance.
While corrective maintenance has its benefits, it's important to acknowledge the potential drawbacks and challenges associated with this approach. Let's explore some of the disadvantages of relying solely on corrective maintenance:
These examples illustrate how corrective maintenance is applied in various industries to address specific equipment failures and ensure the smooth operation of their respective processes.
Food Industry
Facilities
Energy
Hotels
Manufacturing
Healthcare
Transport and Logistics
Maintenance software, such as Computerized Maintenance Management Systems (CMMS) or Enterprise Asset Management (EAM) systems, plays a crucial role in supporting and enhancing corrective maintenance activities. Here are some key ways in which maintenance software aids in the effective implementation of corrective maintenance:
Work Order Management: Maintenance software enables the streamlined management of work orders for corrective maintenance. It allows maintenance managers to create, assign, and track work orders, ensuring that repairs are promptly scheduled and assigned to the appropriate technicians. Work order management features facilitate efficient communication and collaboration among maintenance teams, ensuring that corrective maintenance tasks are executed in a coordinated manner.
Asset and Equipment Tracking: Maintenance software provides a centralized database for recording and managing asset and equipment information. It allows organizations to track the maintenance history, performance metrics, and repair records of each asset. When an equipment failure occurs, maintenance technicians can quickly access the relevant asset information, including manuals, diagrams, and past maintenance tasks, to diagnose and resolve the issue effectively.
Real-time Monitoring and Alerts: Maintenance software can integrate with condition monitoring systems and sensors to provide real-time equipment status updates. By continuously monitoring equipment parameters, such as temperature, pressure, vibration, or energy consumption, the software can detect anomalies or deviations from normal operating conditions. It triggers automated alerts or notifications to maintenance personnel, enabling proactive responses and timely corrective actions.
Spare Parts Inventory Management: Effective spare parts inventory management is critical for timely corrective maintenance. Maintenance software facilitates accurate tracking of spare parts inventory, including stock levels, locations, and reorder points. It helps optimize inventory levels, ensures availability of critical components when needed, and reduces downtime by avoiding delays caused by insufficient or misplaced spare parts.
Data Analysis and Reporting: Maintenance software collects and analyzes data related to corrective maintenance activities, providing valuable insights for decision-making and process improvement. It enables organizations to identify recurring issues, track mean time to repair (MTTR), assess equipment reliability, and evaluate the effectiveness of corrective maintenance efforts. Through customizable reports and dashboards, maintenance managers can gain a comprehensive overview of maintenance performance, identify trends, and make data-driven decisions to optimize their maintenance strategies.
Documentation and Compliance: Corrective maintenance often involves documenting repairs, safety procedures, and compliance-related information. Maintenance software helps capture and maintain digital records of maintenance activities, including work order details, technician notes, checklists, and safety protocols. This documentation not only ensures compliance with regulations and standards but also serves as a knowledge base for future reference, troubleshooting, and audits.
Integration with Other Systems: Maintenance software can integrate with other business systems, such as inventory management, purchasing, or finance systems, to streamline workflows and data exchange. This integration improves the accuracy and efficiency of processes related to spare parts procurement, invoice tracking, and cost management, which are essential for effective corrective maintenance.
By leveraging maintenance software, organizations can enhance the efficiency, accuracy, and visibility of their corrective maintenance activities. It enables streamlined work order management, real-time monitoring, proactive maintenance, data-driven decision-making, and improved compliance. Ultimately, maintenance software empowers maintenance teams to minimize equipment downtime, optimize resources, and deliver timely and effective corrective maintenance solutions.
Corrective maintenance plays a vital role in the maintenance management of industries across the board. While it is reactive in nature, it serves as a crucial component of a comprehensive maintenance strategy when combined with preventive and predictive maintenance practices.
By promptly addressing equipment failures, organizations can minimize downtime, optimize resource allocation, and enhance overall operational efficiency.
Corrective maintenance allows for the timely resolution of unexpected issues, reducing the impact on production schedules, customer satisfaction, and the bottom line.
However, it is important to be aware of the potential disadvantages of relying solely on corrective maintenance. Increased downtime, higher costs, safety risks, and limited equipment reliability are some of the challenges associated with a reactive maintenance approach. To mitigate these drawbacks, a balanced approach that integrates preventive and predictive maintenance techniques is crucial.
By leveraging technology, implementing best practices, and fostering a culture of continuous improvement, organizations can optimize the effectiveness of their corrective maintenance efforts. Clear priorities, efficient work order management, skilled technicians, spare parts inventory management, and root cause analysis are among the key practices that contribute to successful corrective maintenance implementation.
Furthermore, the integration of corrective maintenance with preventive and predictive strategies allows organizations to transition from a reactive to a proactive maintenance culture. This approach helps in minimizing downtime, optimizing costs, improving equipment reliability, and enhancing safety.
As maintenance managers, it is important to evaluate the unique needs of your industry and tailor your corrective maintenance approach accordingly. By doing so, you can ensure the efficient operation of equipment, mitigate risks, and maximize the lifespan of critical assets.
In conclusion, corrective maintenance, when applied strategically and in conjunction with preventive and predictive maintenance practices, is an essential tool for maintaining the reliability, safety, and performance of equipment across a wide range of industries.
By embracing a proactive mindset and implementing best practices, organizations can optimize their maintenance efforts and pave the way for a more efficient and productive future.
Here are some frequently asked questions (FAQs) related to corrective maintenance:
Corrective maintenance refers to the reactive approach of addressing equipment failures or malfunctions after they occur. It involves repairing or restoring equipment to its normal operating condition to minimize downtime and ensure its proper functioning.
Corrective maintenance should be performed when equipment failures or malfunctions are identified. It is triggered by unexpected breakdowns, performance issues, or other signs of equipment failure that require immediate attention.
Corrective maintenance is a reactive approach that addresses failures after they occur, while preventive maintenance is a proactive approach that aims to prevent failures through scheduled inspections, maintenance tasks, and component replacements. Corrective maintenance is performed as a response, whereas preventive maintenance is planned in advance to mitigate the risk of failures.
The advantages of corrective maintenance include cost-effectiveness by focusing resources on equipment that genuinely requires attention, minimized downtime through prompt repairs, efficient resource allocation, enhanced equipment reliability through root cause analysis, learning opportunities for maintenance teams, flexibility in addressing unforeseen failures, and integration with predictive maintenance strategies.
The disadvantages of corrective maintenance include increased downtime during equipment failures, potentially higher costs due to urgent repairs and potential collateral damage, safety risks, unpredictability in planning maintenance activities, limited equipment reliability, negative customer impact, and the risk of perpetuating a reactive maintenance culture.
Organizations can optimize their corrective maintenance efforts by establishing clear priorities, implementing efficient work order management systems, ensuring skilled and well-trained technicians, managing spare parts inventory effectively, conducting root cause analysis for significant failures, fostering a culture of continuous improvement, promoting collaboration and communication, and measuring performance through key performance indicators.
While corrective maintenance is essential for addressing equipment failures, it is not sufficient as the sole focus of a maintenance strategy. It should be complemented with preventive and predictive maintenance practices to proactively identify and mitigate potential failures, reduce downtime, and optimize equipment reliability.
Certain aspects of corrective maintenance, such as work order management and maintenance history tracking, can be automated through computerized maintenance management systems (CMMS) or other software solutions. However, the actual repairs and troubleshooting usually require the expertise of skilled maintenance technicians.
Predictive maintenance uses data analysis and condition monitoring techniques to predict when equipment failures are likely to occur. By integrating predictive maintenance with corrective maintenance, organizations can proactively address potential failures before they cause significant disruptions or downtime, reducing the need for reactive repairs.
Technology, such as IoT sensors, data analytics, and CMMS software, plays a significant role in improving corrective maintenance. It enables real-time monitoring, predictive insights, efficient work order management, data-driven decision-making, and enhanced communication and collaboration among maintenance teams.
See how to plan, execute and benefit from corrective maintenance in different industries.