Neste artigo, exploraremos a fundo como a Manutenção Preditiva, apoiada por IoT e pelas tecnologias de sensores, está a transformar a gestão de ativos na era digital. Discutiremos os seus fundamentos, vantagens e benefícios, bem como a sua integração na Indústria 4.0. Além disso, abordaremos os desafios que as empresas enfrentam na implementação desta estratégia e forneceremos recomendações para maximizar o seu sucesso.
Manutenção Preditiva: Diferença de abordagens
A Manutenção Preditiva envolve a recolha e análise contínua de dados sobre o desempenho e estado dos ativos através de sensores e tecnologias IoT. Estes dados são utilizados para identificar padrões e anomalias que podem indicar uma possível falha ou deterioração no equipamento. Ao antecipar estes problemas, as empresas podem agendar intervenções de manutenção em momentos chave, evitando interrupções inesperadas e maximizando a vida útil do ativo.
Por outro lado, a Manutenção Reativa responde a avarias quando estas já ocorreram, o que pode resultar em períodos prolongados e dispendiosos de indisponibilidade. Em contraste, a Manutenção Preventiva baseia-se em inspeções e manutenção agendadas em intervalos regulares, o que pode levar a intervenções desnecessárias ou à falta de atenção a problemas emergentes.
Manutenção Preditiva vs Reativa vs Preventiva
A Manutenção Preditiva oferece uma série de vantagens significativas em comparação à Manutenção Reativa e Preventiva. Algumas das principais vantagens incluem:
-
Redução de custos operacionais: Ao prever as avarias e agendar a manutenção nos momentos ideais, evitam-se períodos de indisponibilidade não planeados e reduzem-se os custos de reparações de emergência.
-
Maior disponibilidade de ativos: A Manutenção Preditiva ajuda a maximizar a disponibilidade dos ativos ao prevenir falhas e minimizar o tempo de inatividade.
-
Maior eficiência e produtividade: Ao agendar a manutenção de forma inteligente, é possível evitar interrupções na produção e melhorar a eficiência operacional.
-
Maior segurança: A Manutenção Preditiva ajuda a identificar problemas de segurança antes que se transformem em riscos graves para os trabalhadores e o equipamento.
-
Otimização de inventário: Ao antecipar as necessidades de peças de substituição e consumíveis, é possível otimizar o inventário e reduzir os custos.
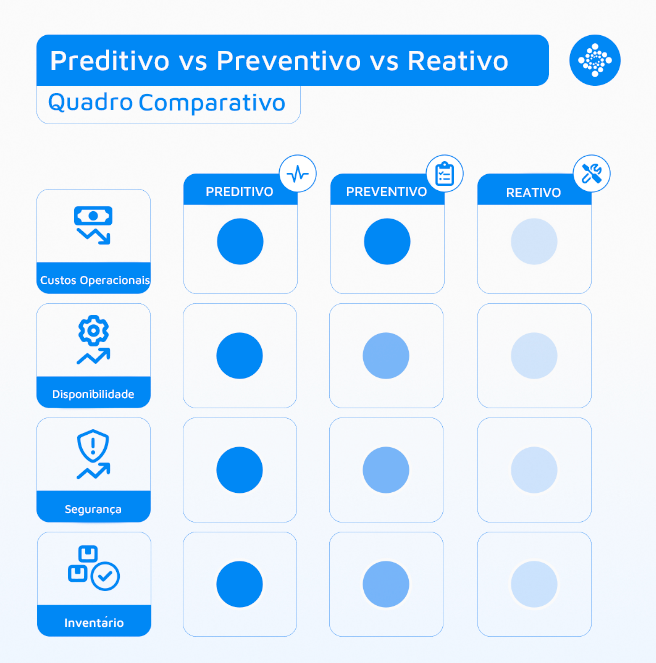
Tecnologias IoT e sensores em Manutenção Preditiva
As Tecnologias de Internet of Things (IoT) desempenham um papel fundamental na Manutenção Preditiva ao permitirem a ligação e comunicação entre dispositivos e ativos, o que possibilita a recolha de dados em tempo real. Estas tecnologias baseiam-se na interconexão de dispositivos físicos através da Internet, permitindo que os ativos estejam ligados e gerem dados constantemente.
Papel do IoT na recolha de dados em tempo real
As tecnologias IoT baseiam-se em sensores e dispositivos inteligentes que estão integrados nos ativos e equipamentos. Estes sensores recolhem dados sobre vários parâmetros, como vibração, temperatura, pressão, nível de fluídos, entre outros. Os dados recolhidos são transmitidos através da rede e armazenados em plataformas de gestão de dados (Armazenamento Cloud), onde podem ser analisados e processados em tempo real.
O papel chave das tecnologias IoT na Manutenção Preditiva reside na sua capacidade de fornecer dados em tempo real sobre o estado e o desempenho dos ativos, permitindo às equipas de manutenção monitorizar constantemente a condição dos equipamentos e dando-lhes a capacidade de detectar anomalias ou alterações no comportamento que possam indicar possíveis falhas.
Descrição dos sensores utilizados na Manutenção Preditiva para monitorizar parâmetros
Os sensores utilizados na Manutenção Preditiva são dispositivos especializados concebidos para medir e monitorizar vários parâmetros físicos nos ativos que são críticos num determinado processo produtivo. Alguns exemplos de sensores frequentemente utilizados nos dias de hoje nas indústrias são:
Sensores de vibração: Estes dispositivos possibilitam a monitorização remota e em tempo real do estado dos ativos graças à sua conectividade. Através da análise espectral, comparam espetros entre diferentes datas ou equipamentos semelhantes, oferecendo múltiplas visualizações, seja em forma de onda ou bandas laterais, bem como um diagnóstico automático para a maioria dos modos de falha da máquina. Alguns sensores, além de fornecerem alertas automáticos em caso de falha, oferecem um diagnóstico completo e orientações sobre como preveni-las.
Um sensor de vibração pode detectar uma ampla variedade de falhas precoces, tais como:
- Desgaste e excentricidade em engrenagens
- Desalinhamento e desequilíbrio
- Folgas mecânicas
- Excentricidade e deformação de eixos
Sensores de temperatura: No contexto da manutenção preditiva, estes sensores desempenham um papel crucial ao monitorizar constantemente a temperatura dos ativos e equipamentos. Ao analisar a temperatura, os sensores podem detectar alterações anómalas que poderiam indicar problemas ou falhas iminentes. Ao detectar estas variações precocemente, as equipas de manutenção podem intervir de forma proativa antes que a situação piore e ocorra uma falha catastrófica.
Um sensor de temperatura pode detectar falhas precoces como:
- Falta de lubrificação
- Sobreaquecimento
- Atrito e fricção
- Mudanças nos modos de operação
Sensores de corrente elétrica: Ao integrar sensores de energia na monitorização de ativos, as organizações podem obter informações valiosas sobre o comportamento e eficiência dos equipamentos em tempo real. Estes dados são usados para realizar análises comparativas e estabelecer padrões de funcionamento normais. Qualquer desvio significativo no consumo de energia pode ser um sinal de um possível problema ou falha, permitindo que as equipas de manutenção tomem medidas antes que ocorra um problema mais grave.
Sensores de corrente elétrica podem detectar falhas precoces como:
- Picos de corrente e quedas de fase
- Consumo excessivo de energia
- Falhas em ligações soltas
- Desequilíbrio de fases
Sensores de pressão: Um sensor de pressão, no contexto da manutenção preditiva, é um dispositivo desenhado para medir e monitorizar os níveis de pressão de fluídos ou gases em equipamentos industriais e sistemas. O seu propósito é fornecer informações em tempo real sobre as variações de pressão nos ativos monitorizados, permitindo detectar possíveis anomalias, desgaste ou deterioração nos componentes.
Sensores de pressão podem detectar falhas precoces como:
- Fugas e obstruções
- Desgaste ou deterioração de componentes (tubagens e válvulas)
- Pressão excessiva ou insuficiente
- Desequilíbrio de carga
Sensores de nível: O sensor de nível é essencial para a manutenção preditiva, pois a sua capacidade de medir com precisão o nível de matéria-prima permite identificar situações anómalas, como perdas de conteúdo, flutuações inesperadas ou níveis perigosamente altos ou baixos. Estes dados são cruciais para prevenir problemas como derrames, sobrecargas ou bloqueios no fluxo de materiais, que poderiam causar danos nos equipamentos, perda de produção ou riscos para a segurança.
Sensores de nível podem detectar falhas precoces como:
- Falhas nas alarmes ou sistemas de controlo
- Desgaste ou corrosão em recipientes e tubagens
- Bloqueios no fluxo de materiais
- Derrames ou fugas
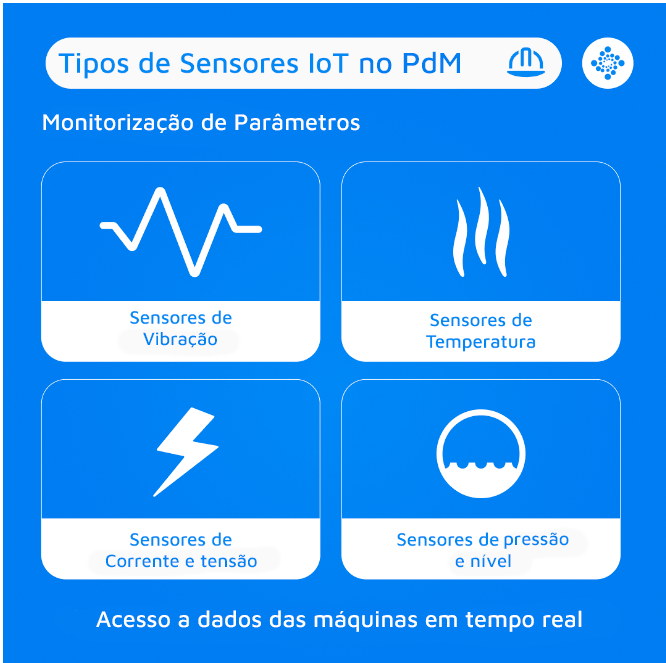
Em suma, a tecnologia IoT e os sensores desempenham um papel crucial na Manutenção Preditiva ao proporcionar dados precisos e em tempo real, permitindo uma gestão de ativos mais eficiente e uma maior disponibilidade dos equipamentos.