Las rutinas de mantenimiento son una estrategia indispensable para el cuidado preventivo de equipos e infraestructuras. Estas rutinas consisten en programar inspecciones específicas para verificar el estado de los equipos y la infraestructura en busca de signos de desgaste o mal funcionamiento.
Su importancia radica en la capacidad de detectar problemas menores antes de que se conviertan en costosas reparaciones, lo que garantiza el correcto funcionamiento de las máquinas y ayuda a evitar tiempos de inactividad no planificados.
Cada instalación requiere inspecciones rutinarias de sus sistemas eléctricos, mecánicos e instrumentales. Estas inspecciones deben programarse, realizarse puntualmente y registrarse utilizando software de gestión de mantenimiento. Es esencial especificar la ruta llevada a cabo en el procedimiento para garantizar una gestión eficiente y documentada del mantenimiento.
La importancia de las rutinas de inspección en el mantenimiento diario
A continuación, te menciono tres aspectos realmente importantes que pueden marcar la diferencia en nuestras operaciones diarias:
Prevenir los tiempos de inactividad: Al inspeccionar periódicamente los equipos, se pueden identificar y rectificar posibles problemas antes de que provoquen paradas inesperadas.
Garantizar la seguridad: Las rutas de inspección ayudan a garantizar que todos los equipos funcionen dentro de las normas de seguridad, protegiendo tanto a los trabajadores como a las instalaciones.
Optimización del rendimiento de los equipos: Las inspecciones constantes ayudan a mantener los equipos en condiciones óptimas de funcionamiento, mejorando la eficiencia y prolongando la vida útil de los activos.
Programación y preparación
Como toda estrategia de mantenimiento, es necesario la planificación, programación, así como la ejecución con los mejores recursos disponibles.
La programación eficaz de las rutinas de mantenimiento son cruciales para minimizar el impacto en las operaciones. Estas deben planificarse durante las horas de menor actividad o cuando interfieran lo menos posible con las actividades normales.
El empleo de un sistema gestión del mantenimiento (GMAO) puede automatizar el proceso de programación, garantizando que las inspecciones se realicen a intervalos uniformes y que no se pase por alto ningún equipo. Además, es necesario considerar la frecuencia de las inspecciones en función del uso del equipo, su criticidad y datos de rendimiento de los activos para optimizar los intervalos de mantenimiento.
Diseño de las rutas de inspección
Diseñar una ruta eficaz es esencial para optimizar el uso del tiempo y los recursos durante las inspecciones. Una ruta bien planificada no sólo minimiza la duración de la inspección, sino que también garantiza una cobertura exhaustiva de todos los equipos críticos. A continuación se explica:
¡Cómo lograr un diseño eficiente de las rutas! Te lo explicamos en 5 pasos.
Paso 1 - Trazar un plano de las instalaciones
Crea un plano detallado y actualizado de las instalaciones. Este plano debe incluir todas las ubicaciones relevantes de los equipos, puntos de acceso y cualquier obstáculo que pueda afectar a la navegación. Utilice herramientas digitales si está disponible, ya que permite realizar ajustes y actualizaciones con mayor facilidad. El objetivo es tener una representación visual clara de las instalaciones, que sirva de base para la planificación de la ruta.
Paso 2 - Segmentar por prioridad y ubicación
En este paso es importante organizar los equipos en grupos en función de dos criterios principales:
Nivel de prioridad: Clasifique los equipos en grupos como críticos, de prioridad alta, media y baja. Los equipos críticos, que en caso de falla podrían causar importantes retrasos operativos o riesgos para la seguridad, deben inspeccionarse con mayor frecuencia.
¿No sabes cómo calcular la criticidad de tus activos?
Proximidad física: Dentro de cada nivel de prioridad, se debe agrupar los equipos en función de su proximidad física para racionalizar el recorrido. Este enfoque reduce los retrocesos y los desplazamientos innecesarios, haciendo que la ruta sea más lógica y eficiente en términos de tiempo
Paso 3 - Optimizar el flujo de rutas
En este caso es importante ajustar la ruta para evitar cruzarse varias veces por el mismo camino, lo que supone una pérdida de tiempo y energía. Por otra parte, con el tiempo tendrás que decidir si tiene más sentido una ruta lineal (del punto A al B) o un bucle (que empieza y termina en el mismo punto) en función de la disposición de las instalaciones y los puntos de entrada y salida.
Paso 4 - Probar e iterar
Una vez establecida una ruta preliminar, realice un recorrido físico para simular el proceso de inspección. Durante esta prueba:
-
Cronometre la ruta y controle el tiempo que se tarda en completar el recorrido. Esto ayudará a programar y determinar si la ruta es factible dentro del plazo deseado.
-
Identifique cuellos de botella y problemas de seguridad. Busque zonas en las que los inspectores puedan sufrir retrasos, como pasos estrechos, zonas de mucho tráfico o peligros para la seguridad, y ajuste la ruta en consecuencia.
-
Reciba opiniones. Los técnicos pueden aportar información sobre posibles problemas que no se hayan detectado durante la fase de planificación, como problemas de accesibilidad a los equipos.
Paso 5 - Aplicar las opiniones recibidas y realizar ajustes
Utilice la información obtenida durante la prueba y los comentarios del equipo para perfeccionar la ruta. Realice los ajustes necesarios en la ruta, la frecuencia de inspección de los activos críticos o el orden de los equipos. Actualice continuamente la ruta a medida que se añadan nuevos equipos o cambie la distribución de las instalaciones.
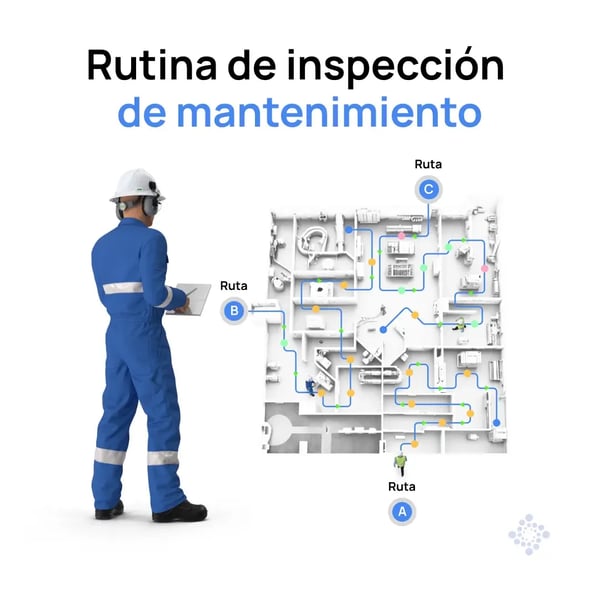
¿Cuáles son las herramientas más comunes dentro de las rutinas de mantenimiento?
En la gestión del mantenimiento es primordial garantizar que tu equipo de inspección esté bien equipado con las mejores y más eficientes herramientas. A continuación encontrará una lista detallada de herramientas y equipos esenciales.
Checklist o listas de verificación
Elabore listas de comprobación detalladas y específicas para cada equipo que guíen a los técnicos en cada paso del proceso de inspección. Estas listas de comprobación deben incluir indicadores visuales, pruebas operativas y métricas específicas que deben medirse.
De ser posible, estas listas deben estar en un formato digital a través de dispositivos móviles que permitan actualizaciones en tiempo real y que puedan estar directamente integradas a los sistemas de gestión de mantenimiento.
Dispositivos móviles
Actualmente la tendencia en el mantenimiento es que los técnicos tengan a su disposición tabletas o teléfonos inteligentes que tengan acceso a un sistema de gestión del mantenimiento (GMAO). Esto garantiza que los inspectores puedan ver e introducir datos directamente en el sistema durante la inspección, acceder a los datos históricos de cada equipo y actualizar los registros de mantenimiento en tiempo real.
Por otra parte, existen dispositivos tienen la capacidad de escanear códigos QR o etiquetas RFID para identificar rápidamente los equipos y acceder a su historial de mantenimiento.
Descubre el poder de las Etiquetas TAGs, NFC y Códigos QR
Instrumentos de medición portátiles
Estos dispositivos se utilizan para medir y registrar diversos parámetros operacionales de los equipos, como temperatura, presión, voltaje, y vibración, entre otros. La función principal de estos instrumentos es facilitar la comparación entre las lecturas actuales y los valores de referencia o estándares previamente establecidos, permitiendo detectar desviaciones o anomalías que podrían indicar una falla potencial.
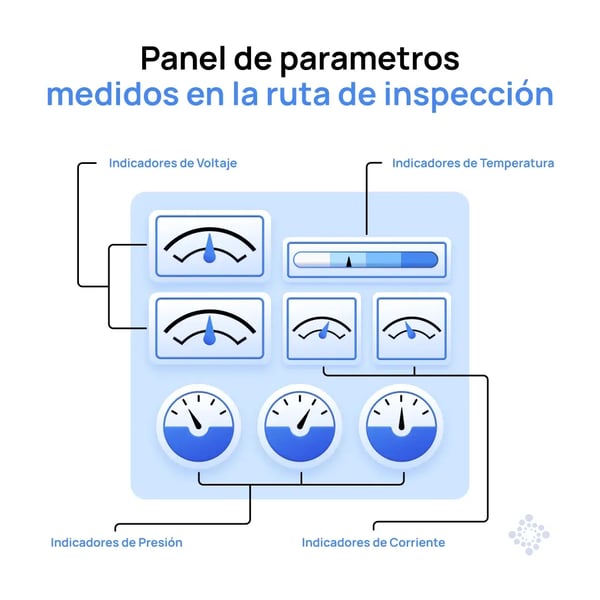
Multímetros: Esenciales para medir valores eléctricos como tensión, corriente y resistencia, ayudando a diagnosticar problemas eléctricos, como picos de tensión o consumo de energía elevado.
Cámaras termográficas: Usados para detectar puntos calientes en componentes mecánicos o eléctricos que indiquen un elevado aumento de la temperatura.
Analizadores de vibraciones: Fundamentales en el análisis de máquinas rotativas para detectar desequilibrios, desalineaciones o fallas en los rodamientos.
Detectores ultrasónicos: Usados para comprobar fugas de aire, fugas de gas o la integridad de las juntas soldadas, que pueden ser cruciales para mantener sistemas presurizados.
Conoce más sobre las técnicas de mantenimiento preventivo
Equipos de protección personal (EPP)
Proporcione equipos de seguridad estándar como cascos, gafas de seguridad y guantes. Asegúrese de que cumplan las normas de seguridad más recientes aplicables a su sector y al entorno específico de sus instalaciones.
Dependiendo del entorno, pueden ser necesarios EPP adicionales como protección auditiva, mascarillas de respiración o ropa ignífuga.
Conoce los aspectos claves al momento de seleccionar tus EPP
Resolución de los problemas detectados
El proceso de resolución de los problemas detectados durante las rutas de inspección es fundamental para el protocolo de mantenimiento. Implica acciones inmediatas, una comunicación eficaz y un seguimiento diligente. A continuación se explica cómo optimizar cada paso.
Acciones inmediatas
Una vez identificado un problema crítico, el primer paso es evaluar la gravedad y el impacto potencial en las operaciones y la seguridad. Aplique medidas inmediatas para evitar que el problema avance a un estatus de alta gravedad. Esto puede implicar el apagado de los equipos, el aislamiento de la zona afectada u otras respuestas de emergencia según la situación.
Si procede, aplique soluciones temporales para mitigar el problema hasta que puedan llevarse a cabo reparaciones permanentes. Esto podría incluir parchear fugas, puentear ciertas funciones o utilizar sistemas de reserva. Solo recuerda, deben ser de carácter temporal.
Informes y comunicación
Documente rápidamente el problema con todos los detalles, incluyendo fecha, hora, el equipo implicado y una descripción detallada del problema y de las medidas temporales adoptadas.
Notifique el problema abriendo una solicitud de orden de trabajo utilizando los canales de comunicación disponibles en tu compañía. Puede ser mediante llamadas directas, correos electrónicos o un sistema de gestión del mantenimiento.
Las reparaciones deben programarse estableciendo prioridades en función de la gravedad del problema, asegurándose de que todos los recursos, como piezas y personal, se organizan con antelación para evitar retrasos.
Una vez finalizadas las reparaciones, verifique la eficacia de las medidas adoptadas. Para ello, se debe volver a inspeccionar el equipo y, si es posible, hacerlo funcionar en condiciones normales para asegurarse de que funciona correctamente.
Actualice los registros de mantenimiento en el GMAO para reflejar las reparaciones realizadas, incluyendo detalles del problema, la solución aplicada y la fecha de resolución. Estos datos históricos son muy valiosos para la futura planificación del mantenimiento y el análisis de tendencias.
El futuro de las rutas de inspección está cada vez más interrelacionado con los avances tecnológicos, especialmente con la integración de sensores del Internet de las Cosas (IoT), análisis predictivos y otras innovaciones digitales. Estas tecnologías están llamadas a transformar la forma en que se planifican, ejecutan y optimizan las inspecciones de mantenimiento.
A día de hoy permiten reducir la frecuencia de las inspecciones físicas o desplazamientos hacia áreas peligrosas, ya que proporciona el monitoreo de parámetros de forma remota. Los sensores detectan anomalías e identifican patrones que pueden indicar posibles fallas en los equipos en su fase inicial.
Existen algoritmos de IA que pueden predecir con mayor precisión las fallas en los equipos, reduciendo la dependencia de la intervención humana, automatizando ciertas decisiones de mantenimiento basadas en datos históricos y tendencias.